No products in the cart.
How to Secure Pallet Racking
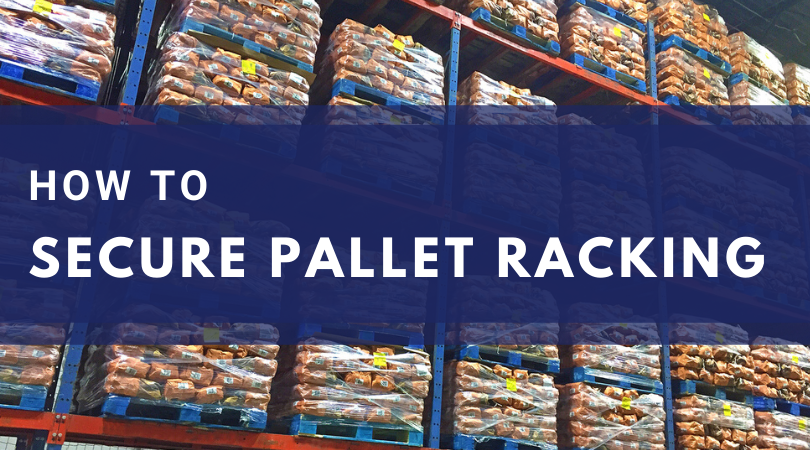
20
Apr
Pallet racks are excellent storage and organization solutions for warehouses of all sizes. Pallet racking offers a convenient and highly economical way of storing and accessing pallets and is typically simple to configure. Your pallet racks may hold numerous pallets, requiring anchoring and regular inspections to minimize the likelihood of dangerous accidents.
Pallet rack anchors can help counteract excessive weight and uneven weight distribution. There may also be local building codes, internal workplace regulations and OSHA pallet rack anchor requirements to consider. Knowing how to anchor pallet racks is essential for warehouse managers to ensure compliance and keep warehouse employees and products safe.
View Our Pallet Racking Solutions
Do Pallet Racks Have to Be Anchored?
OSHA does not explicitly list pallet racks as a requirement, but that doesn’t mean it isn’t advisable or necessary. You may not “have to” do it, but anchoring pallet racks contributes to overall warehouse safety and operational processes. Leaving pallet racks unsecured presents significant risks, including:
- Disorganization.
- Potential local building code violation.
- Lost or damaged products.
- Expensive repairs to equipment or products.
- Injuries to employees, some of which could be fatal.
A free-standing rack holding significant weight is a serious risk to the people in your warehouse and represents a financial liability. An unsecured pallet can overturn, costing thousands of dollars in damaged inventory. Working with the pallet manufacturer or a pallet rack professional to install and anchor your racking system can help eliminate these risks.
OSHA Pallet Rack Anchor Requirements
Although the OSHA pallet rack requirements may seem vague, they potentially fall under multiple OSHA standards, including:
- The OSH Act of 1970 Section (5)(a)(1): This OSHA General Duty Clause states that employers must provide a safe workspace for employees, free from recognized hazards that could cause physical harm or death. It’s reasonable to assume that a falling pallet represents a significant hazard, which means OSHA expects some foresight. An average pallet rack is large and heavy enough to cause severe injury, and proper anchoring removes that risk and promotes employee well-being. This standard can also be applied to regular pallet rack inspections and adhering to weight limits to promote ongoing safety.
- OSHA Standard 1910.176(b): This standard covers the secure storage of materials and states that any materials stored in tiers should be stable and secure. Storage of materials should not create a hazard, and unsecured racking presents significant risks. The standard also requires tiered storage to be stable and secure against sliding and collapse, which includes anchoring it to the floor.
Creating a safe workspace that aligns with OSHA requirements means anchoring your pallet racks and securing pallet rack uprights, as even without implicit instruction, doing so is imperative to the safety of your warehouse employees and products.
Tips for How to Secure Pallet Racking
The best method for anchoring and securing pallet racks depends on several factors, including:
- The age and type of pallet rack system you have
- The weight limit and load capacity of each rack
- The warehouse environment, including floor material and layout
- The specific pallet rack manufacturer requirements
With various types of pallet anchors available, choosing the right one for your application is critical for the safest possible work environment. Some common types of anchors for pallet racks include:
- Concrete screws: You can remove these anchors, which could be useful in some situations. However, what makes them easy to remove makes them prone to pulling out if something strikes or lifts the column base. Concrete screws are threaded, which means they widen the hole when they pull out, making it unusable for future anchors.
- Strike anchors: Strike anchors contain a pin with a wedge at the bottom, which expands when you strike the anchor with a hammer. They’re easy to install and remove, but you must replace them after removal and have limited tension.
- Wedge bolts: Wedge bolts are robust, easy to install and have higher embed depths, making them ideal for securing pallet racking.
Most racking base plates have multiple holes to accommodate bolt placements. Ensure you follow original equipment manufacturer requirements for the number of anchors and fasteners specifications.
To anchor warehouse racking securely, you need to have an action plan, understand and abide by all manufacturer instructions and check that all fittings are tight.
Make a Plan
Have a design in place before installing your warehouse racking system. If your warehouse is large enough, consider working with an engineer to determine the best way to use the space. As you draft your initial plan, consider the following:
- Will you use new or used pallet racks?
- What additional storage solutions, such as shelving, will you incorporate into your warehouse?
- What local building codes must you follow?
- Would adjustable pallet racks make sense for your space?
- What are the dimensions of the area, considering any overhead ducts and lightning?
- Are you leaving adequate space on either side of the pallet racks for safe walking and convenient forklift access?
- Do you require aisle protection for additional safety?
- What is the distance from your unloading spot to the pallet racking system?
While you can take every possible measure to ensure workplace safety, your team should also know how to avoid hazards. Have an ongoing training plan to teach workers and management how to use pallet racking. Your training program should cover proper storage procedures, including how to store and secure items on the racks, retrieve items manually or with a forklift and any unsafe actions they should avoid when near the storage racks. In addition, ensure your workers have access to the instructions for maintaining the weight limit on each rack and avoiding overhang.
Implement a labeling and records system to streamline your process. Label each storage rack with durable labeling material, making finding and retrieving the goods there easier. Keep a record system of any incidents, concerns or suggestions from workers. A warning and consequence system should also be in place for workers who fail to use pallet racks responsibly.
Ensure you train each new employee on these procedures and update or reengage training as any changes or challenges arise.
Follow Manufacturer Instructions
All pallet racking and storage systems come with instructions from the manufacturer, which include the weight limit, installation instructions, safety recommendations and other useful information. Because each manufacturer designs and crafts racks differently, it is essential that you follow these instructions and refrain from do-it-yourself solutions or shortcuts.
Following all manufacturer instructions ensures a stable installation that operates within any potential warranties. If you combine pallet racks and storage solutions from multiple manufacturers, follow the instructions included with each. For a used pallet rack system, try and find installation protocol and anchoring recommendations on the manufacturer’s website. You can also use a rack ID guide to help you figure out what kind of equipment you are working with.
These manufacturer instructions are where you will find specific requirements and recommendations for securing pallet racking to the floor, including the best method for anchoring and what supplies you need.
Ensure a Level Frame
Concrete warehouse floors often have irregularities. Leveling your frames helps to distribute weight evenly on your pallet racks and prevent unnecessary wear and tear on your pallet anchors. You can use steel or plastic shims to get your uprights level and avoid affecting your racking system’s integrity.
Focus on Embedment Depth
The deeper your pallet rack anchors are embedded into the warehouse floor, the more stable your pallet rack. Discuss your options with your provider to ensure you choose the best embedment depth.
Space Your Anchors
Despite appearances, concrete can be brittle, and placing your anchors too close together can impact the stability of the ground. Keep enough distance between each anchor to ensure there is enough concrete surrounding each one.
Tighten Fittings
Once you’ve installed your racking system, tighten all fittings and anchors — including those on the beams, floor racks and decking — before you begin using racks for storage. This final step will cover any areas you may have overlooked during the initial installation. Make a point to inspect and tighten these same fittings regularly, as they may loosen as your team moves product on and off of the racks each day.
Consider installing pallet rack accessories to protect your system and minimize how often you need to repair or replace parts.
Inspecting Your Pallet Rack Systems for Security
Regularly scheduled inspections are crucial for the longevity of your pallet rack system and the safety of your employees. Here is what you need to know about pallet rack inspections:
Who Should Perform the Inspection?
The owner or manager of warehouse operations is responsible for implementing and adhering to a regularly scheduled inspection plan conducted by a qualified person. OSHA defines a “qualified person” as someone with a degree, certificate or professional standing or someone with extensive knowledge, training and experience, as well as a successful demonstration of the ability to solve and resolve problems related to the type of work in question.
Someone qualified to inspect a pallet racking system includes professional pallet rack installation services and providers or representatives from the racking manufacturer.
In addition to a regular inspection conducted by a qualified person, designate a manager or team of employees to perform regular, self-guided inspections. Train a safety officer to know what areas to inspect and implement proper protocols for repairs and replacements. Incorporating self-inspections into your maintenance routine lets you identify potential issues or areas for concern before they become more costly or hazardous problems.
When Should Inspections Happen?
Depending on the type of inspection and the specific situation, you should conduct inspections at regular intervals, including:
- Weekly walkthroughs: Your safety management officer or team should conduct a thorough walkthrough of the entire pallet rack storage area. They should visually inspect all locations listed below, documenting and reporting any concerns so you can correct them as soon as possible. Consider working with your professional inspector to create a checklist of areas your safety team should inspect during weekly walkthroughs.
- Annual inspections: Schedule a professional pallet rack safety inspection at least once yearly. Trained professionals have more experience and knowledge of rack system safety and may identify additional problems. When scheduling a professional inspection, prepare to answer a few questions about your warehouse, including dimensions, types of pallet racks installed, the name of your pallet rack manufacturer, other storage and shelving present and all current and former concerns.
- Post-damage inspections: Schedule a professional inspection immediately after any repairs, damage or safety incidents. Even minor dents can throw off the load balance of your racking system.
- Post-alterations: Schedule a follow-up inspection if you rearrange, restructure, downsize or expand your warehouse. Any time you move or adjust your rack system, it is imperative that key areas be re-inspected for safety and functionality.
Which Areas Should Be Inspected?
A professional inspector will check specific areas during an official inspection, but you and your safety officer should also focus on certain points during self-guided checks, including:
- Bending and breakage: Visually assess whether all racks, beams and crossbars are straight and level without bowing, bending or breaking. Perform a closer inspection of possible bowed areas with a straightedge ruler. Some deflection is normal but watch for signs of overloaded racks.
- Rust and corrosion: Note any spots of corrosion, rust or discoloration. If water or excess moisture is causing the corrosion, take steps to fix the issue. If from friction or rubbing against other racks or pallets, reorganize and space your products to avoid future corrosion.
- Bolts and screws: Inspect that each screw and bolt is secure and not coming loose, and plan to replace any damaged or missing screws.
- Anchors and bracing: Inspect the integrity of all anchors, baseplates and bracing and retighten as needed. Every baseplate should have at least one anchor.
- Shims: If you’ve used shims, ensure they’re in good condition. Any shims between two to six times the anchor’s diameter should be locked by welding or adding a second anchor.
- Locks and connectors: Check that all beam connectors and safety locks are secure without visible damage.
- Netting and protectors: Inspect netting and protectors for breaks or corrosion, and make sure that any welding is intact.
- Unsafe modifications: Note any temporary modifications or quick fixes present, such as steel beams holding up racks. Temporary modifications are hazardous and must be corrected immediately.
- Labels: Check and replace any worn labels as needed. Note whether your team uses the labels and organizes the racks according to weight and product. Ensure the load rating information for all racks is clearly visible.
When Should You Conduct Repairs and Replacements?
Regular weekly and annual inspections are only the first steps in ensuring a safe workplace. For those inspections to be effective, you must take immediate action to repair, replace and correct all issues. Keep an organized record of all damage and repairs so you can track changes over time. If an inspector informs you of a potentially hazardous concern, cease operations in that area until the problem is remedied. A trained professional can help you decide whether a damaged rack requires a simple repair or an entire system replacement.
Some situations that may call for rack replacement include:
- Extensive damage: Look for signs of irreparable damage, like heavy rust and bent or busted beams. Minor damage is usually a quick fix. In some cases, it may not impact your workday at all.
- Outdated equipment: Warehouses often need updated equipment to perform optimally. If your equipment is outdated or no longer serves warehouse and material needs, it could be time for a replacement.
- Expansion or downsizing: If you’re making a significant change in your warehouse, the storage racks may need adjustments or replacements.
Visit T.P. Supply Co for Pallet Racking Products and Services
Anchoring and securing your pallet racking system is the best way to keep your employees safe and ensure smooth daily operations. After installation and anchoring, be sure to schedule regular weekly and annual inspections of your racking system and make prompt repairs or replacements to avoid workflow interruption.
T.P. Supply Co has everything you need for pallet rack installation, including:
- Pallet rack uprights and beams
- Husky racks and wire
- Pre-configured and universal tear-drop systems
- Unarco interchangeable beams and uprights
- Double-slotted pallet racks
- Used and refurbished pallet racks for budget-conscious companies
- Wire mesh decking and pallet rack accessories
- Pallet rack installation and warehouse design services
In addition to pallet racks, T.P. Supply Co. offers material handling, safety and security, shelving and storage solutions.
If you have questions about securing your pallet rack systems or want to discuss a pallet rack installation or design consultation, contact our experienced staff today. You can also visit us online to learn more about T.P. Supply Co pallet racks, material handling and storage solutions, or use our customized quote tool to request a custom quote.