No products in the cart.
Comparing Pallet Sizes and Styles
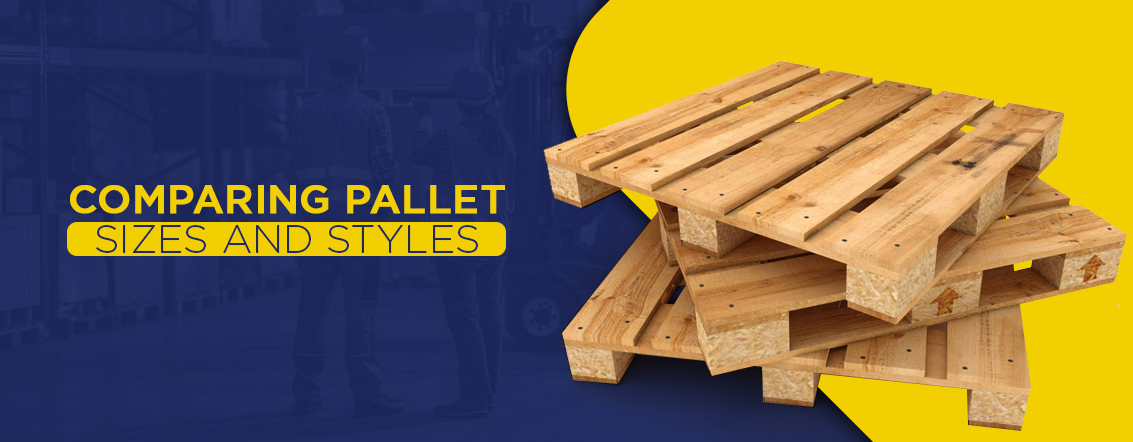
11
Feb
When you run a warehouse, lots of decisions affect your operation’s efficiency and profitability, as well as the overall safety of your facility. One major consideration that warehouse managers must address is how the warehouse will use its pallets and pallet racking systems to optimize material handling and inventory management.
View Our Pallet Racking Solutions
Pallets and pallet racking go hand-in-hand. You need the right size of pallet racking to ensure you can safely and securely store your goods. Likewise, you also need the right size pallets that will safely carry your loads and fit on your pallet racking properly. If you’re looking to invest in new pallets or install new pallet racking, this guide to pallet sizes and styles will help you make the right decision for your warehouse needs.
What Is the Size of a Standard Pallet?
Pallets come in a variety of sizes and styles, and different industries have different standards for their average pallet size. Within the freight shipping industry, the standard pallet size is considered to be 48 inches deep by 40 inches wide. These standard pallet dimensions were first set by the Grocery Manufacturers Association (GMA), which is the world’s leading authority on the shipping of consumer packaged goods. In fact, this organization is so influential that it’s not uncommon to hear standard pallets referred to as GMA pallets. Though 48-by-40 inches is considered the standard pallet size, there are other common pallet dimensions to be aware of when determining the right pallet racking solutions for your warehouse. Squared pallet dimensions also include the common 42-by-42 inches and the larger 48-by-48 inches. When referring to non-squared dimensions, such as with the standard 48 inches deep by 40 inches wide, the width refers to the pallet’s side that runs parallel with the front of the rack, while the depth refers to the side view of the pallet when positioned on the rack. It’s important to know the variety of pallet dimension options available to you so you can select pallets and pallet racking systems that accommodate your particular goods. Having pallets that are too small for your shipment sizes causes goods to hang over the edges of the pallet, creating a bulky and non-uniform shipment, effectively defeating the purpose of palletizing your goods. On the other hand, if you’re using pallets that are too big for your typical shipment size, you’ll be wasting precious warehouse and cargo space. Be sure to select the right pallet size or purchase multiple runs of sizes if you’re handling a variety of goods. Having a standard pallet size in your warehouse is crucial for space management, as uniform pallets stack and store more easily than varying pallet sizes. Since space is a critical commodity in any warehouse, be sure to select a pallet size that you can adhere to so you can optimize your warehouse’s space and overall efficiency.
What Is an Oversized Pallet?
An oversized pallet is any pallet that’s considered bigger than the standard pallet size. Since there are so many custom pallet designs out there, there are potentially unlimited dimensions that would be considered oversized. Because the term “standard” varies from industry to industry, there are no universal oversized pallet dimensions. For the grocery industry, oversized would be anything larger than the standard 48-by-40 inches. Some pallets can be several feet wide or long, and these are designed for special applications for shipping large and bulky items, such as home appliances or furniture. Oversized pallets can also refer to the freight company’s definition of a pallet that’s larger than the standard pallet dimensions they ship. In these cases, oversized pallets are measured to calculate freight surcharges. Shipping and managing oversized pallets can become quite costly when charged a surcharge fee each time. To prevent oversized pallets, always use pallets that are large enough to safely and securely ship or store your goods.
Types of Pallet Styles
In addition to the variety of pallet dimensions, there are also other differences between pallet types. Different styles of pallets have different applications and uses and are manufactured for particular industries and situations. As such, they may also require unique racking and material handling solutions to ship and receive them. Broadly, there are two main pallet types based on materials — wood vs. plastic pallets. Wood pallets were the original pallet type and are still the largest pallet style in circulation today. The standard wood pallet size is the same as any pallet — 48-by-40 inches. However, like all pallets, wood pallet measurements also vary depending on the industry and application. Despite how common wood pallets are, they’re quickly being replaced by sanitary plastic pallets, which are required in many industries, including agriculture, food and cold storage as well as pharmaceutical supplies. More specifically, pallet styles differ by how they’re constructed. The following are the five common pallet styles you’ll see in the freight shipping industry.
1. Stringer Pallets
Stringer pallets are constructed using a sandwich design where the top and bottom decks are separated by stringers, or boards that are typically 2-by-4-inch or 3-by-4-inch wood, plastic or metal beams, depending on the pallet. These stringers help support the unit load by acting as crossbeams that evenly bear and distribute the weight. While stringer pallets can be designed in many size variations, the most common size for stringer pallets is 48-by-40 inches, or the standard GMA size pallet. The most common pallet style in the U.S., stringer pallets have a uniform design so forklift tines can access the pallet from either the front or the back. This gives stringer pallets a desireable two-way design for convenient material handling and management. In some cases, stringer pallets will be notched or chamfered on the non-accessible sides, so that forklifts and pallet jacks can access them from all four ways. Compared to other pallet styles, stringer pallets aren’t typically considered to be quite as durable as some other styles, and therefore, aren’t used for shipping particularly heavy goods. However, this largely depends on the quality of the pallet’s construction.
2. Block Pallets
Similar to stringer pallets, block pallets are constructed in a sandwich design, where nine to 12 solid material blocks are placed between the top and bottom decks of the pallet. The blocks are placed in all four corners of the pallet, in the center of each side of the pallet and then another one to three in the middle of the pallet, acting as its central unit load support. Because block pallets use smaller blocks rather than full-length boards, block pallets are considered four-way pallets, as they are accessible by forklift and pallet jacks from any side. Depending on the manufacturer, block pallets can be designed with solid bottom decks or open decks. Block pallets are commonly thought to be more durable than stringer pallets, but this can vary based on construction quality. Block pallets can be made from wood, plastic or metal.
3. Double-Face Pallets
Double-face pallets are another type of pallet design where the pallet has a deck on both the top and the bottom. Double-face pallets are designed to be extra durable. Having a deck across both the top and the bottom of the pallet makes it stronger and able to support a load more evenly. Double-face pallets can be either reversible or non-reversible. Reversible double-face loads are built so that they can be loaded on either the top or bottom sides as both decks are constructed the same. With non-reversible double-face pallets, the bottom side is less durable than the top, and therefore, can only be stacked one way.
4. Double-Wing Pallets
Double wing pallets are a type of double-face pallet. They have a deck on both the top and bottom sides of the pallet, but the decks extend beyond the pallet’s edges or stringers, giving the appearance of wings. Double-wing pallets are typically two-way pallets but can be four-way if they have notched or chamfered stringers. Depending on the construction, double-wing pallets may be reversible or non-reversible. Double-wing pallets come in standard sizes and other varieties and are generally made from wood, but may also be available in plastic.
5. Solid Deck Pallets
Solid deck pallets are constructed with a solid top deck that doesn’t have slats. Solid deck pallets are generally made from wood, where the deck is a solid sheet of plywood. Solid deck pallets may also be available in plastic or metal. Solid deck pallets are convenient for warehouses shipping smaller goods, as the solid design prevents items from slipping through the cracks. Many companies also like solid deck pallets because their clean design makes them look better. Solid deck pallets are also much easier to clean and convenient to transport.
Finding the Right Size Pallet Rack for Your Pallets
The size and weight of your goods will determine what type and size of pallet you need to most effectively transport or store your items. Once you know the pallet size you will use, the next step is to choose the correct pallet racking solution that can support your pallets’ dimensions and load weight. Therefore, to choose the right pallet rack for your pallets, you need to consider both the pallet racking dimensions and the rack’s load capacity. Not all pallet racks are created equal. Different applications require different pallet rack sizes and designs. Additionally, your particular warehouse standard operating procedures and layout will also play a role in determining how to configure your pallet racks. By choosing the right pallet rack, you’ll improve your operational efficiency, protect your palletized goods and keep your workers and equipment safe from accidents. To determine the right size pallet rack for your pallets, follow these tips:
- Determine your pallet size: The first step to choosing the right pallet racking dimensions and configurations for your warehouse is to know your pallet size. Whether it’s the standard GMA pallet or another pallet, be sure to get accurate pallet dimensions as this will determine the dimensions of your pallet rack.
- Calculate your load size: In addition to the width and depth dimensions of your pallet, you’ll also need to factor in your standard pallet size height. Because each pallet load will vary depending on the goods shipped, there is no universal or average height of a pallet load. The combination of pallet width and depth with load height determines your overall load size. Once you know how tall your average pallet load is, you can calculate the distance between each row of beams. Always ensure you have enough space between the top of the pallet load and the beam above to ensure proper clearance room when the forklifts or pallet jacks are placing or removing loads.
- Choose the right rack depth: Your pallet’s depth will determine how deep your rack should be. As a rule of thumb, you want your pallets to have a three-inch overhang beyond the beam to improve forklift or pallet jack accessibility.
- Consider the distance between uprights: You can customize your pallet rack configuration by determining how many pallets you want to place on each racking row. Decide whether you’d like to store one, two or three pallets per row, and this will determine the distance between each rack upright.
- Select the right wire decking: Once you know your pallet rack specifications, you can now determine the right gauge of wire decking. This is the final step in configuring your pallet racking as the wire decking needs to be fitted to the racking system based on the dimensions of the beams and uprights.
Another factor to consider when finding the right pallet racking system for your pallets is the total available vertical space in your warehouse. Knowing how tall your warehouse ceilings are will help you determine how high to take your pallet racks. You should always try to maximize the amount of vertical space in your warehouse for better efficiency and scalability as your inventory grows. Keep in mind that fire codes will determine how high you can take your racking, as you must allow up to 2 feet of clearance between the top of your highest load and the ceiling or nearby fire suppression sprinklers. When selecting the right pallet racking system for your warehouse, always consult a pallet racking expert. An experienced supplier can help you determine the right pallet racking specifications and configuration for your load sizes and other operational needs.
Choose T.P. Supply for Your Palleting Racking Needs
Choosing the right pallet racking system for your warehouse is a critical decision, and there are lots of factors to consider. You don’t want to end up with the wrong pallet racking that won’t adequately and safely support your loads. To prevent unsafe pallet racking installation, work with an experienced pallet racking supplier who will customize the right solution for you. When searching for your next pallet racking system, choose T.P. Supply for your racking and material handling solutions. With an extensive inventory of sturdy and durable double-slotted pallet racks and teardrop pallet racking systems, T.P. Supply will help you find the right racking systems to efficiently organize your warehouse and safely protect your inventory. For more information on finding the right pallet racking systems for your warehouse, contact T.P. Supply today. Call us at 1-877-302-2337 or contact us online for a free quote.