No products in the cart.
Maximizing Vertical Warehouse Space
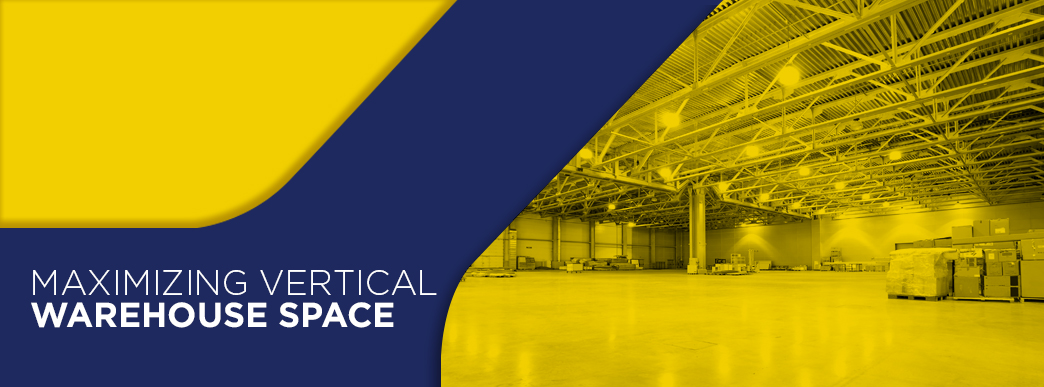
31
May
Warehouse managers are tasked with the important responsibility of continuous improvement to preserve and grow the company’s bottom line. Managers know there are lots of ways to make the company more profitable, whether that’s by investing in the right tools to increase worker productivity, streamlining processes to promote efficient picking, packing and loading or coming up with creative storage solutions when bringing on new product lines.
All of these approaches contribute to a much more efficient and smooth-running operation. But what happens when the biggest challenge a warehouse manager or operator faces has to do with space constraints? How can you create more space out of thin air? Lots of businesses may naturally start looking for extra real estate to lease or buy because it seems like the obvious solution. If you want to reduce the risks and costs associated with taking on additional warehouse space, it’s wise to assess your current warehouse layout and systems first and look for opportunities to capitalize on the existing space. For most warehouses, this means going vertical.
Tips for Increasing Vertical Warehouse Space
While growing businesses are thrilled to stock more inventory to sell, it also leads to a new set of challenges. Though it might be a desirable problem to have, a growing warehouse also means that managers need to think outside the box and look for ways to maximize their current space to prevent having to move or lease additional real estate.
Expanding your storage units upwards ensures you’re taking advantage of all the cubic feet you’re paying for. Moving goods upwards means you can free up floor space below too. You can use free floor space to add in more storage units, invest in more material handling equipment or give workers more space at their workstations.
If you’re looking to maximize your warehouse space so you can increase your storage capacity, it’s essential to take advantage of vertical space. Vertical space is widely underused in warehousing management, and it’s valuable cubic footage you’re paying for but not using. But before making any major changes to your inventory management, consider the following practical steps when getting started with maximizing warehouse space utilization.
1. Review Existing Vertical Space
The first step in maximizing your storage is to assess how much vertical space you’re currently underutilizing and how much more you can capitalize on. This means measuring your warehouse heights to get a more accurate idea of the actual amount of usable space. An industry rule of thumb is that once your warehouse hits 80 percent inventory capacity, it has reached its max. That’s because managers must take into account empty overhead and aisle space necessary for safety and compliance reasons, which should be set at a minimum 20 percent of capacity.
When assessing your vertical space opportunities, don’t forget to take into account ceiling and sprinkler clearances. These are critical for complying with fire and safety codes. The National Fire Protection Association requires 18 inches of vertical space between the top of a shelving unit and its contents and the ceiling. Always consult an engineering firm before making any big layout changes to ensure your operation is up to code.
At this phase, it’s also an excellent opportunity to look at your warehouse floor plan. If you’re planning on stacking your inventory vertically, you’ll likely need to invest in new storage units that are conducive to vertical storage. You may end up overhauling your existing layout to adapt to the new vertical approach, such as making new aisle widths that accommodate forklifts. Because of this, you may also consider rearranging your layout for minimum aisle widths. Make sure you know where all mechanical and electrical units are as these will factor into your new layout and where you can place your new storage structures, especially when placing them against walls.
2. Take an Inventory Audit
Once you’ve determined that vertical storage is the right solution for your warehouse, the next step is to assess your current inventory. Some people may perceive vertical storage as a drawback because it makes top-shelf items less easily accessible. To avoid this drawback, warehouse managers need to think strategically about where to place their inventory in a new vertical system.
By conducting an inventory audit, warehouse managers can identify items that should take up the top-level space. Consider which of your items have slower sell-through rates, are seasonal or are less frequently accessed. Naturally, these items should be placed higher up, leaving frequently accessed goods on the lowest shelves. Auditing your inventory will help you determine which items you want to keep closer to the floor or at ground-level and which products should remain higher up.
3. Invest in Vertical Storage Systems
Going vertical in a warehouse requires the right equipment designed to free up floor space and safely house inventory. Pallet racks are universally considered the simplest and most efficient method for increasing vertical space in warehouses. These industrial shelving units are designed to store palletized goods in multiple rows, primarily facilitating first-in, first-out (FIFO) inventory management systems. Accessible either by forklifts or manually, pallet racks are adjustable and can be made to fit your warehouse heights as well as the types of products you stock.
Going vertical with sturdy pallet racks makes stocking and picking much more convenient for workers. It also makes the warehouse safer, both by keeping items protected from overcrowdedness and by giving workers better accessibility to goods picked repeatedly.
4. Leave Room for Future Needs
When investing in new vertical storage solutions, you should also consider your company’s future needs. While it’s impossible to predict the future, you can use your recent growth trends as a gauge to determine how much vertical storage you may need in two to five years.
Will you be storing greater inventory levels of certain products or equipment? Will you be downsizing any offerings down the road? Thinking about the future direction of your warehouse inventory can help you make smarter decisions today without creating more problems later on. Investing in more vertical storage, like pallet racking systems, upfront can help you save on having to purchase additional units in a few years.
Use Pallet Racking Systems to Maximize Vertical Space
One of the simplest warehouse space optimization techniques is to use industrial pallet racking units. Pallet racking systems are designed to maximize vertical space by taking advantage of available overhead areas. Pallet racking standardizes your inventory management, ensuring that all products are benefiting from the same shelving frames and widths, making it easier to operate material handling equipment efficiently and consistently.
There are a few typical pallet racking types. In general, all pallet racks allow you to store palletized or containerized goods on horizontal rows and on multiple levels. How pallet rack types vary is in their design, ease of adjustability and function they ideally serve. At T.P. Supply Co, we offer the following types of pallet rack solutions that allow you to maximize your warehouse vertical space.
1. Selective Pallet Racking
Selective pallet racking, also known as standard racking, is the most common type of pallet rack system used in vertical storage. Made of two vertical steel frames known as uprights connected by rows of two horizontal load beams, selective pallet racking is designed to hold pallet loads safely. The load beams are often covered by wire mesh decking, which offers an additional layer of stability and prevents small items from falling through. Accessible from either side of the rack, selective pallet racks enable workers to retrieve pallets and goods from the front or back. Their one-deep design means that selective pallet racks allow workers to retrieve pallets and products without needing to move other pallets out of the way.
2. Teardrop Pallet Racks
Teardrop refers not to the design of the rack itself but to the way the cross beams are secured to the uprights. Teardrop-shaped holes in the uprights securely fasten the teardrop beams to the structure. Teardrop beams are easy to lift and pull from the uprights and reposition if you want to increase or decrease your shelf height. Teardrop pallet racks are designed to be universally compatible with other storage solutions, parts and brands. If you’re looking for flexible, versatile and easy-to-assemble pallet racking, consider implementing teardrop pallet racks as part of your new plan for maximizing warehouse space.
3. Double Slotted Pallet Racking
If you’re handling large and heavy pallet loads, double-slotted pallet racking was designed for your warehouse needs. Compared to teardrop pallet racking, double-slotted pallet racking is a vertical storage solution designed to be exceptionally sturdy. As its name suggests, double-slotted pallet racking refers to load beams that are secured to uprights by two slots. These high-quality pallet racking systems are also easy to adjust but made with heavy-duty materials meant to withstand the toughest industrial settings. If you’re counting on sturdiness and security from your vertical storage solution, then double-slotted pallet racking might be the right rack style for you.
When moving forward with a new vertical storage plan, it’s essential to invest in pallet racking or any form of shelving unit that meets the various codes they’re subject to. Racking needs to be in place to support load weights and be structurally sound enough to meet seismic codes and other restrictions. Warehouse managers must do their due diligence when choosing pallet racking systems to increase vertical storage capacity. Partnering with material handling experts like T.P. Supply Co is the best way to ensure your racks perform how you need them to while keeping your people and products safe and secure.
Pallet Racking Components and Accessories
Pallet racking systems consist of multiple components all working together to make a strong, dependable and functional vertical storage system. This includes pallet rack accessories and extensions that help further support loads, protect goods and building structures and stabilize the rack units. At T.P. Supply Co, we offer the following accessories and solutions to accompany your vertical storage solution:
- Wire mesh decking:Â Wire mesh decking is a welded metal layer added to pallet racks. This is a popular pallet rack accessory to enhance load capacity and meet certain local codes.
- Column protectors: Going vertical means more use of motorized material handlers, which increases the risk of structural damage. Column protectors keep your building’s structure safe from damage.
- Crossbars:Â A staple component of any pallet racking system, crossbars are designed to withstand pallet loads. Our sturdy crossbars come in 36-inch, 42-inch and 48-inch lengths.
- Double flanged pallet supports:Â In some cases, you may need additional support bars, like double flanged pallet supports, that stop overloaded pallets from falling between the load beams.
- Hat-style pallet supports: Another additional support option, hat-style pallet supports are an alternative style to double flanged pallet supports used when you don’t have slots accessible.
- Structural pallet support:Â Our structural pallet supports are a standard 42-inch length appropriate for box beam and channel beam crossbars.
- Row spacers:Â Choose from 6-inch, 8-inch, 12-inch and 18-inch row spacers that help ensure consistent spacing between pallet rack rows.
- Wall spacers:Â Our 6-inch, 9-inch and 12-inch wall spacers help make sure there is a consistent distance between your racking systems and the supporting wall.
Material Handling and Safety Equipment for Vertical Storage
When going vertical, there are other considerations beyond choosing vertical storage solutions like pallet racks. Warehouse managers must shift the entire warehouse ecosystem to support the new vertical storage solution. Being able to access goods stored on shelves higher up means you need the right material moving equipment to place and retrieve these goods safely.
Given your warehouse is now reaching new heights, your workers will likely need forklifts capable of retrieving pallets from top shelves. For non-palletized goods, such as items stored in containers, totes or boxes, workers will need scissor lifts or rolling ladders to help them reach the top shelves.
OSHA’s 4-foot fall protection rule means that workers accessing items 4 feet or higher above ground must be secured. Guardrails and fall protection equipment are essential to keeping workers safe and ensuring your facility is compliant with OSHA regulations. Though going vertical requires additional planning and prevention measures, T.P. Supply Co is here to help you implement a new vertical storage system with multiple solutions to improve efficiency and keep your people and products safe.
Contact T.P. Supply Co for Pallet Racking
If you’re ready to take advantage of valuable vertical space in your warehouse, choose to partner with T.P. Supply Co. As material handling and warehouse solution experts, we offer your business the complete package in vertical storage systems. From pallet racking, wire mesh decking and accessories to lift tables and guardrails, we’ll ensure your warehouse is well-equipped to implement a successful new vertical storage plan.
Since 1979, T.P. Supply Co has worked with warehouses and distribution centers to implement simple, effective storage solutions that improve operational efficiency and safety. Our preconfigured racking systems are proven vertical storage solutions that help you maximize your facility’s cubic footage. Choose from our wide selection of new, used or reconditioned pallet racking systems that meet your needs and your budget. We always deliver our products on our own trucks and offer installation by our in-house crew.
Contact T.P Supply Co today to learn more about the best vertical storage systems for maximizing your warehouse space. Call us at (877) 302-2337, or you can reach us online.