No products in the cart.
Differences Between Racking and Shelving?
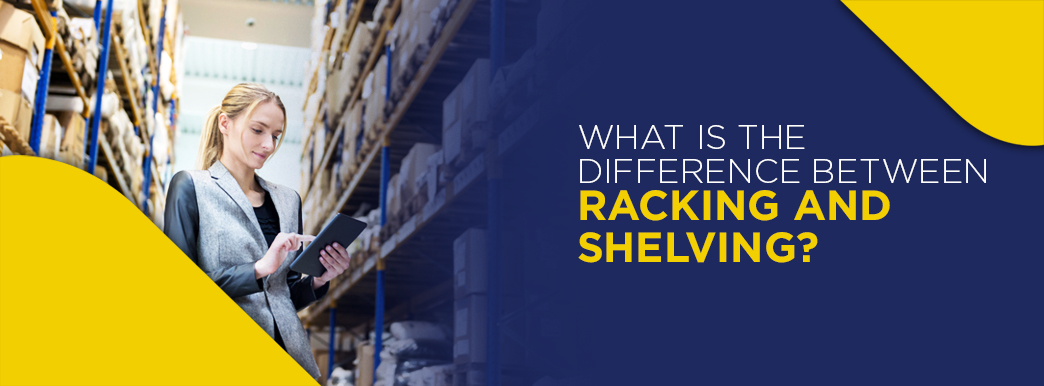
29
Jul
Table of Contents
- Understanding Industrial Shelving and Racking
- Types of Industrial Shelving
- Types of Industrial Racking Systems
- Industrial Shelving Vs. Pallet Racking
- Choosing the Right Storage Solution for Your Business
Racking and shelving are storage solutions that help businesses manage their inventory storage needs and maximize floor space. Both solutions allow you to store, organize and display different sizes, shapes and types of items. They can be customized to accommodate your unique stocking needs while ensuring your industrial or commercial facility remains organized, safe and highly productive.
The differences between racking and shelving are not easy to identify, especially because they’re utilized in most of the same ways. However, they typically differ in their design, construction, application and accessibility. A deep dive into the benefits and uses of industrial shelves and racks reveals major differences that make it crucial to choose the right system for your specific purposes.
Understanding Industrial Shelving and Racking
Shelving and racking are often used interchangeably despite the two types of storage solutions having distinct differences.
What Is Industrial Shelving?
Industrial shelves are flat horizontal surfaces supported by wall mounts or brackets to hold a variety of objects and materials. They’re often used in residential or commercial settings to store, organize and display lightweight items such as books, accessories, clothes and electronics. Shelves have a limited storage capacity but they are easily accessible, allowing people to pick up things from them easily by hand.
Industrial shelving is available in a variety of materials, sizes and shapes to fulfill the specific needs of different users. Shelving often comes with accessory options, such as drawers, bins, baskets or dividers to improve functionality. There are four main types of industrial and commercial shelving to consider, each with unique benefits and potential drawbacks.
What Is Industrial Racking?
Industrial racking is a specialized storage system designed to hold and organize palletized items in a vertical position. Racks have multiple levels and horizontal bars stacked on top of one another and supported by steel beams or aluminum poles. They have a higher weight capacity, which makes them capable of holding heavy and bulky items without sagging or bending.
Specialized lifting equipment like cranes, forklifts and shuttle carts are used to load and unload racking systems. Industrial racking systems are made from heavy-duty materials and are sometimes freestanding structures within an existing warehouse. More often, racking systems are fixed to the floor or walls of the industrial or commercial facility for extra strength and protection.
View Our Industrial Storage Options
Different Types of Industrial Shelving
There are four main types of industrial and commercial shelving to consider:
1. Industrial Steel Shelving
Steel shelving is the most obvious choice for many applications due to its strength and relatively low cost. As long as you put it together correctly — which is simple to do — you’ll get years of service from a steel shelving unit.
Steel shelving is available in different gauges. You can purchase shelves with higher weight capacity for storing cases of heavier items and save some money by getting a higher-gauge shelf setup for employees or customers to grab unboxed items. There are two main types of steel shelving:
- Closed shelving: These shelves have panels that cover the sides and back of the unit. Closed shelving is more durable and aesthetically pleasing than open shelving. They are best placed back to back or up against walls rather than freestanding.
- Open shelving: These shelves replace panel backing with braces that create needed stability. With this design, employees can access the items they need from any direction.
While closed shelving is more likely to come in standalone units, open shelving has the advantage of being somewhat modular. For example, you can connect multiple shelving units with extended support braces, creating one large shelving run.
Some advantages of industrial steel shelving include:
- Easy assembly
- Customization and availability of accessories
- Suitable for high-density storage
2. Industrial Wire Shelving
When looks matter, wire shelving is the way to go. Wire shelves can accommodate a wide range of products in commercial and industrial applications. They also facilitate airflow, which is essential, especially when handling food and other sensitive products.
Wire shelving has numerous safety advantages, like the fact that it barely collects dust. The open wiring allows water from fire sprinklers to reach the products placed on the shelves in case of a fire outbreak. Wire shelves are also much easier to move than other shelving types because they are lighter-weight and offer straightforward assembly. The main disadvantage of wire racks is that they are less durable than the other industrial shelving options.
Some advantages of industrial wire shelving include:
- Lightweight and can become mobile if mounted on casters
- Easy to keep clean due to lack of dust collection
- Ideal for high-visibility products
3. Rivet Shelving
Rivet shelving is also referred to as boltless shelving since its assembly doesn’t require any bolts. It’s often the most economical shelving option, and they have the distinct advantage of being incredibly easy to assemble, using only a rubber mallet to align rivets and slide them into the frame.
Other than their utilitarian appearance, the primary downside to rivet shelves is that they are constructed using heavy-gauge steel. This makes them extremely heavy, which may make it difficult to move around when you want to reconfigure your storage space. Rivet shelving is not a great option if you need bells and whistles like drawers or dividers to get the most out of your shelves.
A few advantages of rivet shelving are:
- Budget-friendly
- Quick, straightforward assembly
- Suitable for stockrooms, warehouses and nearly any other industrial application
4. Widespan Shelving
Widespan shelving bridges the gap between shelving and racking solutions. They are broader and sturdier than other types of shelving and are ideal for situations where you need to store a lot of heavy products without automated material handling solutions. For instance, if you operate a warehouse with a vast range of products but only sell them in small quantities, employees will need to hand-pick the items.
Widespan shelves have the highest load capacity of all your options and can often hold up to 2,000 pounds on each shelf. This form of storage is best for bulky items, making it one of the best warehouse shelving racks, but it is not suitable for pallets or compatible with forklifts.
Advantages of widespan shelving include:
- Huge weight capacity
- Ideal for storing large items
- Front and back item accessibility
Different Types of Industrial Racking Systems?
Warehouse shelving racks are an essential part of keeping pallets organized and accessible when you need them. There are five main types of industrial racking systems to consider.
View Our Selection of Pallet Racking
1. Selective Rack
This is the most common type of industrial racking system found in almost all warehouses. It consists of two vertical frames with shelf beams in between. Selective racking allows workers to stack one pallet deep. Companies that use this storage solution generally either place racks up against a wall or arrange them back to back.
This racking is “selective” because every pallet in the system is accessible without having to move anything else out of the way. It’s an excellent solution for convenience but not ideal if you need to store a high density of pallets.
These racks are either bolted or welded together. Welding by the manufacturer is the preferred assembly method, as it reduces liability and provides a more durable solution. Warehouses can use selective racks in almost any environment with any size and weight of product. If you have low turnover along with high differentiation among products, selective racks are a good option.
The advantages of selective racking are:
- The most economical option
- Easy reconfiguration
- No need for specialized lift vehicles
2. Double-Deep Racking
This type of racking involves having two rows of selective racks placed one behind the other. Warehouses commonly use this configuration to rack two pallets with the same product in a single slot that spans both racks. Employees need a lift truck with an attachment for double-deep handling or a deep-reach lift truck to retrieve pallets from the back rack.
Although double-deep racking is technically one configuration of selective racking, it’s a form of high-density storage. The higher density your racking is, the better you can optimize your warehouse space. You can store more pallets per cubic foot, but the system is less flexible than standard selective racking. You would not want to use this storage system if you didn’t have enough of the same product to fill both the front and back slots of a double-deep rack.
Some advantages of double-deep racking include:
- Lowest cost per pallet position among high-density racking options
- Greater use of available space
- Easier access than other high-density options
3. Drive-In or Drive-Through Rack
As another form of high-density racking, drive-in or drive-through storage systems have a design that accommodates lift trucks. Rather than using a shelf beam between vertical frames, these systems employ rails that extend the full length of the rack. Lift trucks can drive right into the rack structure to drop off and pick up pallets. Depending on your needs, you can get drive-in or drive-through racking that can hold two, three or more pallets.
- Drive-in racks: These have an entry point that doubles as the exit, so they work best for applications where the last inventory in goes out first.
- Drive-through racks: These racks have two entry points, making them ideal for first-in, first-out inventory applications.
One of the things to remember about this type of racking system is that lift trucks can cause the structure to sustain more impact than racks that don’t need lift trucks. Whether it’s a new operator making mistakes due to inexperience or a more senior crew member bumping into a rack by accident, you want to be sure you purchase a high-quality racking system that will stand up to everyday use.
A few advantages of drive-in and drive-through racking are:
- Takes up fewer aisles than selective racking
- Allows storage of up to 75% more pallets than selective racking
- Only marginally more expensive than double-deep racking
4. Pushback Rack
A pushback rack system is more complex and has more moving parts than other forms of racking storage. It consists of a progression of carts that nest within each other and move back and forth on rails. When a worker has a new pallet to deposit, they will push the current pallets backward and load the new pallet in the next position. When it’s time to retrieve a pallet, the one behind it moves forward so it’s ready for extraction.
Pushback racks are excellent if you have a lot of different stock-keeping units (SKUs) and require many pick faces to operate efficiently. If you do bulk storage and store many of your products in groups of five pallets or more, this is an excellent storage system choice.
These are the advantages of pushback racking:
- Offers storage density similar to drive-in racking but with better selectivity
- Can reduce picking time
- Faster to unload and load than drive-through and drive-in racking
5. Flow Rack
Pallet flow or gravity flow racking is the best solution for first-in, first-out storage systems. This rack uses wheels or rollers that carry pallets down an incline, allowing workers to pick them up when they stop at the other end of the system.
Flow racking allows you to store loads back-to-back, removing the need for aisles. One of the benefits of this is that you don’t always need a forklift, so you can free up the equipment to do something else. Another pro of flow racking is that it operates on gravity, thereby reducing energy costs.
Advantages of pallet flow racking include:
- Eliminates the need for aisles, replacing them with lanes
- Can go as deep as you need it to
- Ideal for warehouses with high throughput
Industrial Shelving Vs. Pallet Racking
Industrial shelving and racking systems are essential storage solutions in warehouses, offices and storage centers. While the terms are often used interchangeably, they have numerous distinct differences that make them suitable for different purposes, environments and situations.
Cost
The costs of industrial shelving and racking vary significantly based on the size, design, quality and materials used. Generally, shelves are more affordable than racking because of their simple design. This means racks require a significant investment because of their specialized design and higher weight capacity.
Load Capacity
Racks are tougher or more heavy-duty than shelves. They are typically used to store heavy and bulky goods stores in pallets. Their construction also factors in their need to withstand impact by lift trucks. The multiple levels and horizontal bars on the racking allow them to withstand significant weight from heavy machinery, tools and appliances. Shelves are made of lighter materials and are not capable of holding as much weight as racking.
Space Utilization
Shelving is typically available in smaller units than racking because it’s used to store lightweight inventory that people can carry around by hand. Racks are significantly larger because they’re designed for storing large and heavy items. However, racks maximize vertical space, which allows them to provide more storage on the same floor space.
Racking is designed to be utilized in large warehouse spaces, so it takes up a lot more floor space than shelving. Fortunately, while racks take up a lot of floor space, they allow easier access to the stored space than shelving. Racks utilize vertical height to increase cubic density. They are typically deeper, wider and stacked higher than shelving.
Ease of Access
Shelving systems allow warehouse operators to organize and retrieve inventory by hand. While you can utilize them to store items on the same level as racks, it’s harder to retrieve items stored on the top shelves or deeper on a shelf. Racks help organize items according to purpose, size and type, which makes it easy to locate goods.
Access is made even easier and more convenient with the use of material handling equipment, such as cranes, pallet trucks, forklifts and lift trucks. These equipment reach significant heights and carry heavy loads, making it simpler to move inventory in and out of the racks. Access to shelves is limited by an operator’s height, while racks can be as high as safely possible.
Application
Industrial racking systems are typically customized to meet a business’s unique needs. They are most suitable for big warehouses handling heavy and bulky items that require specialized equipment to be moved around. Shelving is suitable for small businesses without products but may also be used alongside racking to manage storage in big companies effectively.
Choosing the Right Storage Solution for Your Business
Shelves and racks are good storage options for many businesses, but they both have their strengths and weaknesses. The right one for your specific business depends on the type, size and weight of products you handle. You must also consider other factors, such as your available space, desired accessibility, cost, durability, ease of customization and maintenance needs.
Generally, shelves are a good option if you need to store light and flat items that can be easily handled by human operators. However, racking is the better choice when you deal with heavy, bulky or awkward items. They’re also highly customizable, which makes them ideal for storing irregularly shaped and sized items.
Shelves are sufficient for light commercial or residential use where the space is limited and there’s a need to access items frequently. Racks are the best option for large commercial and industrial settings where products are stored and distributed as large pallets of goods. These settings include warehouses, storehouses, logistic centers and factories.
Storage Solutions From T.P. Supply Company
Whether you’re still exploring different types of racks and shelves or you’re sure and ready to invest in a more efficient storage solution for your business, come to T.P. Supply Company. We pride ourselves on service and solutions that have resulted in more than 90% of our customers returning for repeat business, and we’re ready to provide the right storage for your unique needs.
Whether you’re in the market for just a couple of shelves and a rack or two or are looking to save money by ordering in bulk, we are happy to meet your needs. For more significant projects that require innovative answers, our customized quote tool allows you to share your vision and get a quote for your ideal system. Contact us today and we can make it happen.