No products in the cart.
Inventory Storage Management for Small Businesses
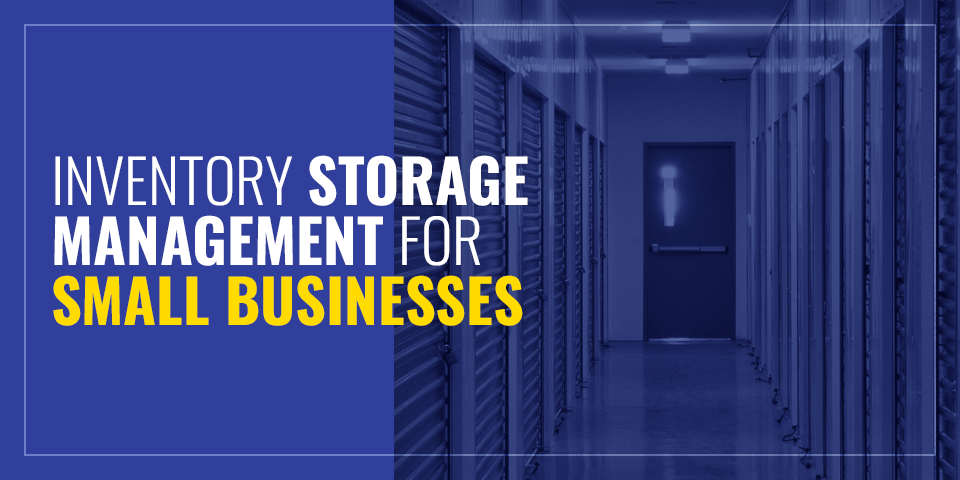
18
Dec
There are over 30 million small businesses in the U.S., so you can bet there is a lot of a variety represented in that number. No matter what your company sells or how you sell it, one thing is sure: You have inventory. Some companies are small enough that they can keep all their inventory in a storage room in their retail location, or in a small warehouse if it’s an e-commerce business. Other small businesses may need larger storage facilities or warehouses to hold inventory.
No matter how much inventory you have or where you keep it, managing your inventory well is key to the success of your business. Properly managing your stock helps you satisfy customers, maximize profits and avoid headaches. Small business inventory storage can seem overwhelming at times, but with the proper storage and organizational practices, you can manage your store’s goods like a pro.
What Is Inventory Management?
Inventory management comes down to being aware of what you currently have in stock, where to find it and what to order when. It involves three main components:
- Diligent organizing
- Detailed record-keeping
- Careful strategizing
Organization permeates all aspects of inventory management, but it plays a tangible and pivotal role in your inventory storage. Inventory takes up space, and you should use that space in the best way possible. Arrange the items you have in stock in a way that is intuitive, consistent and accessible. If your inventory is not well organized, the other parts of the inventory management process become more difficult.
Detailed record-keeping is necessary because, especially if your business is doing well, inventory never remains static for long. New items are constantly coming in and going out. Each time a customer makes a purchase from your business, that’s at least one less item in your inventory. Every time a truck comes in delivering more stock, that’s many more items in your inventory.
So how do you keep track of it all? Very small businesses may figure out how to manage inventory effectively by using a digital spreadsheet or even a physical notebook. Most companies quickly outgrow this method, however. Even if you have the time and manpower to sustain this process, it still limits you. For one, this manual method doesn’t offer any analytics to show you which items are selling the most frequently, and which are not moving and may no longer need to be among your product offerings. That means you have to make those calculations yourself.
If the manual method is no longer practical for your business, you’ll want to keep track of your inventory digitally. You can do this through a point-of-sale system equipped for inventory management or through an inventory management software program. In both cases, software can keep track of each item through scanning the barcode or SKU code. You label and scan items into the system when you first add them to your storage facility or warehouse, and you scan them again when someone purchases them.
Whether you keep records manually or digitally, it’s essential to use these records to make predictions, then make smart decisions based on those predictions. What is selling like hotcakes and needs reordering in larger quantities or more frequently? What isn’t selling much at all? Ill-managed inventory can result in storage shelves overflowing with unwanted product or an out-of-stock notice that disappoints customers and loses you business.
Inventory Storage Options and Equipment Needed
Now that we’ve established the basics of inventory management, let’s walk through the door of your storage facility. This is where your inventory is, and it’s where much of the behind-the-scenes work goes on to make the sales that happen online or in the storefront possible. In a moment, we’ll look at tips for how to organize inventory for small businesses, but first, let’s talk about some practical aspects of storing your inventory.
Businesses that don’t have a storage plan in place typically default to stacking boxes or bins of inventory on the floor. This method, known as block stacking, doesn’t make efficient use of space, however. In a recent post, we discussed a few more efficient storage organization methods you can use. These include:
- Using pallet racks — With pallet racks, which come in a variety of types, you can take advantage of vertical space and keep your inventory in pallets.
- Using fixed shelving — Shelving is a great way to keep lighter inventory accessible and off the floor. You can use space horizontally or vertically.
- Using a pallet flow design — Also called carton flow, this method is expensive, but it allows you to take advantage of depth to keep the oldest inventory in the front and the newest in the back.
How to manage inventory for small business depends on your needs. Here are a few questions to ask yourself as you try to determine the best way to store your inventory:
- How much space do I have to work with in my storage facility?
- Do I have vertical space I can take advantage of, in addition to horizontal?
- What shelving or racks would support the weight of my inventory items?
- Does it make sense for me to store inventory in pallets, in boxes or out loose?
- What is the shelf life for items in my inventory?
- Which products should be most easily accessible?
If your storage is part of a warehouse used for packaging, shipping or other enterprises, this will also influence the way you set up your inventory storage. For shipping purposes, it makes sense to arrange it so your most popular products are closest to the shipping area.
If you sell an imperishable product, shelf life may not matter much, but if you sell a product that has a finite shelf life, it’s smart to use a setup that is conducive to the FIFO method. FIFO stands for first-in, first-out, meaning older items that entered your inventory first are also the first to sell, rather than remaining on shelves while newer versions of the same product get sold.
A pallet flow setup is designed to facilitate this method, but if your inventory storage is small and doesn’t use pallets, you can use freestanding shelves and have a system for taking products from one end, and adding new ones to the other end.
However you choose to lay out your storage facility, there are some basic supplies you need to store inventory effectively:
- Racks or shelving — Unless you’re going to block-stack your inventory, you need either racks or shelving. You may choose to use a combination of both if you have some heavier items you want to stack in pallets, and lighter items you’d prefer to shelve. If you use shelves, you may want to also add bins to your supply list so you can keep items orderly.
- Hand trucks and service carts — These pieces of equipment help you move bulky items in your warehouse or storage facility. Both hand trucks and service carts are on wheels, allowing you to roll items from point A to point B across the floor. Dollies can also perform a similar function, though they don’t include a handle for steering.
- Lift equipment — If you have heavy items you need to also be able to move vertically, you’ll need some lifting equipment. A pallet jack can help you move pallets. A lift and tilt table can make jobs like sorting or labeling easier, since it allows the operator to raise and tilt a box of items. Depending on the size of your operation, you may even want a forklift to help you move items and place them up on shelves.
- Rolling ladders — Unless you and your employees can reach the top shelf in your storage facility on your own, you need a way of getting up there. Rolling ladders allow you to access higher shelves anywhere in your facility. Choose a ladder that gives you the height you need, whether just a foot or 15 feet, and fits into your space.
- Labels — Labels are important throughout your inventory storage area. Especially if you store items in bins, you need labels on each bin to show what item it contains. You want workers to be able to tell what item is in each container at a glance and to know precisely where new items go as they come in.
- Safety equipment — If you have stacked heavy objects anywhere near where people will be working, you want to be aware of any safety hazards and do what you can to keep employees safe. Fortunately, safety equipment like aisle shields, rack guards and guardrails can help you do just that. Never compromise when it comes to safety.
Now that we’ve gone over the basics of inventory management and storing your inventory, let’s look at five tips you can use to help you organize your inventory more effectively.
1. Do a Physical Inventory at Least Once a Year
Using inventory management software is smart, but it still leaves room for error. After all, people still have to scan items for them to get counted. The software itself could also experience a glitch. To make sure you know exactly what you have on hand, you should conduct a physical inventory at least once a year — though biannually or quarterly is even better. This process involves physically counting every item in your inventory. To prevent complications, you should cease other operations in storage during the time of the physical inventory.
2. Keep Storage Clean and Orderly
How can you keep track of inventory and find a certain product when you need it if your storage is in disarray? It’s extremely important to keep your storage area orderly, regardless of its size. This one may seem like a no-brainer, but it’s easy to let things become disorderly over time. Especially when you add new products to your inventory, if they don’t have a designated place, your workers may end up putting them haphazardly wherever they fit.
Old items that won’t sell can end up taking up permanent residence in a corner somewhere. To prevent this problem, have a clearance sale to get rid of these items — otherwise, you’ll just be storing them indefinitely. People love sales, and you need an orderly storage facility where you can be confident you are using every bit of space.
In addition to being orderly, you also want to make sure to keep your storage facility clean. Accumulated dust and dirt present a health hazard for employees, and they may settle in places where you don’t want it, like on the products you plan to sell. You might want to hire someone or designate an employee to clean your storage facility periodically.
3. Update Storage Layout Annually
Successful small businesses grow and change over time. Are you selling the same products this year as you were this time last year? Probably not. As you find which items don’t sell and which do — a vital aspect of inventory management — and as you create or discover new items you know your customers will love, the products in your storage facility will change.
Because of this fluctuation, reevaluate at least once a year to make sure you are still using the optimal organization and layout for your storage facility. It’s especially vital to do so if your company packages and ships items from your facility. If you have newer items that sell like crazy, but they’re not in the most accessible place, move them to be more accessible. Make sure employees familiarize themselves with any changes to the layout and organization of the facility so they know where to find things.
In some cases, you may find a new layout calls for new equipment. Perhaps you didn’t use pallets before, but now you do, and you need a pallet rack. Instead of relying on methods you’ve outgrown, intentionally take time to determine the best way to store and organize your current inventory every year. After you’ve done this, make an updated map to show where items are.
4. Label Receptacles With SKU and Photo
You want employees to know what’s in each bin immediately. You could use a label maker to make small labels with a product’s SKU on it. However, the best way to label boxes and bins is with the SKU number of the item along with a photo. Even if someone doesn’t remember a certain SKU, they are sure to recognize a picture.
To keep these photos vibrant and in good shape, laminate them. If you’re placing labels directly on bins, affix them to the bin using adhesive-backed Velcro. The fastener will hold the photo on securely, but it also allows you take it off and replace it with a new photo if you need to repurpose the bin to hold a different item. You can also affix labels to the shelf to show all bins in a given row or stack contain a certain item.
5. Hire an Inventory Manager If You Need One
Depending on the size and scope of your business, handling inventory management may be something owners or general managers don’t have adequate time for. Since this is such a crucial aspect of your business, you should give it all the time it needs. If you can’t do this, it’s a good idea to hire an inventory manager — someone who can dedicate their focus to managing your inventory with excellence.
Before you hire externally, you may want to think about your existing staff and determine if anyone has shown the diligence and wisdom to manage your inventory well. If you hire a current employee, make sure you still provide training, though you won’t need to spend as much time as you would showing the ropes to a new employee who is completely unfamiliar with your storage facility and with the products you sell.
Contact T.P. Supply Co for Inventory Storage Solutions
If you need supplies to outfit your storage facility, T.P. Supply Co has you covered. For four decades, we’ve provided the best storage solutions for our customers, and we’re confident we can do the same for you. In fact, over 90 percent of people who buy from us become repeat customers! When you order from T.P. Supply Co, you can also take advantage of our installation services to ensure everything gets professionally installed in your warehouse or storage facility. Call us at 877-302-2337 or contact us online today!