No products in the cart.
Efficiently Using Your Warehouse Storage Space
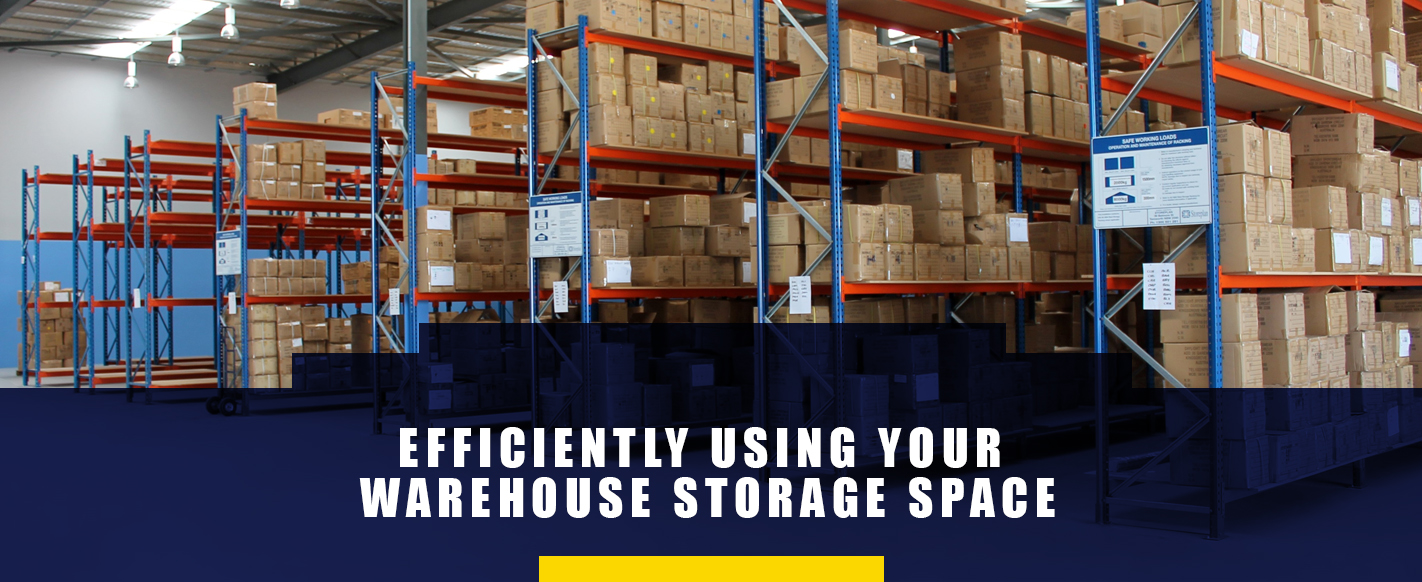
01
Nov
Maximizing warehouse storage space can be a significant challenge for facility managers and operators. Making the most of available floor space and room volume seems a lofty mark for warehouse owners. Effective product storage and retrieval efficiency are the goals all warehouse people try to achieve, yet it often seems unobtainable. It doesn’t have to be so.
The first key to unlocking warehouse space utilization is proper planning. The second key to freeing warehouse space optimization is selecting the right equipment. It’s combining these two principles that make your warehouse space management successful.
When you seem to run out of room in your warehouse, you have three choices. First, do you relocate to a larger facility? Second, do you reduce inventory? And third, do you find creative ways to increase existing warehouse capacity?
Maximizing Your Warehouse Storage Space
Relocating to a larger facility is rarely an option for most warehouse companies. It requires a large capital investment and a significant amount of time in selecting, relocating and reorganizing an already busy business. Reducing inventory is also a poor choice as it limits the potential to fulfill customer orders. For most warehouse organizations, finding creative methods to improve efficiency in their existing facility is the ideal solution.
In evaluating your current warehouse operation, you’ll wonder what maximum warehouse capacity really is. Supply chain consultants find that when a warehouse reaches 80 to 85 percent of storage utilization is when efficiency in movement and storage declines. In other words, you might consider 80 to 85 percent capacity as a good guideline for your warehouse’s top end.
These experts go on to describe their findings that warehouse space typically accounts for 15 to 20 percent of per-order costs. By these figures, we can calculate that 20 percent of space inefficiency could reflect as much as five percent your cost-per-order. If you’re in a big warehouse with large throughput volume, that figure of inefficiency could have a significant impact on your profits.
Clearly, there’s a lot to be gained by carefully planning your warehouse layout and equipment. That includes your product storage tools like bulk racking systems, cantilever racks and pallet racks as well as industrial shelving and storage systems.
Main Warehouse Functions and Storage Needs
In general, four main functions happen in every warehouse facility. It doesn’t matter if you operate a large, medium or small facility. These primary functions remain consistent:
- Storing products: This can range from warehouse storage solutions for small items to large-scale solutions for high-volume pallets loaded with similar materials. Each application requires storage solutions unique to their characteristics.
- Inbound operations: Every product in your supply chain has to arrive and find storage, including receiving and returns. You’ll find your best efficiency in reducing travel time and minimizing inbound operation trips. Generally, high turnover items need the shortest distance and time for inbound product placement.
- Outbound operations: Picking and staging are two main outbound operations. How you select your options and implement your storage systems will have a profound effect on outbound product handling. You need storage racks and shelving that are durable, efficient and safe while being easy to access.
- Value-added processes: No doubt you have value-added processes as part of your warehouse production. That might include labeling products, additional packaging measures or some special kitting process. No matter what customer value-added service you supply, you’ll need efficient space and equipment for it.
Let’s look at the types of storage options for warehouses that you can implement for warehouse layout best practices.
Types of Storage Options for Warehouses
Effective warehouse storage options should address these primary functions. Your objectives are to use space efficiently, allow access for effective material handling equipment, provide excellent storage-to-cost ratios, have maximum flexibility to meet changing needs and do this within the best and safest housekeeping model. It sounds like an impossible challenge, but it’s not if you use the right storage options.
To accommodate these warehouse functions and maximize your efficiency, you need to know what storage solutions and system designs you have available. There are a few main storage system options universally used in the warehouse industry. Not all will be ideal for your operation necessarily, but let’s examine the four most common systems:
1. Bulk Storage
Floor stacking or bulk storage is your most basic option. It’s the simplest and usually requires the least investment, but it can also be the most inefficient use of space. Bulk storage requires no physical storage equipment like racks or industrial shelving. Products sit directly on the warehouse floor and are arranged in horizontal depths. Depending on product durability, pallets might be stacked two or three high. Bulk storage has no efficiency for vertical cubing or elevated storage. You can consider bulk storage as a starting point before graduating to more effective systems.
2. Pallet Racks
These are upright storage frames connected in various methods. The idea is housing individual pallets in vertical applications without direct stacking. With pallet racks, you can isolate loads with inbound and outbound operations without moving or disturbing another loaded pallet. Typically, pallet racks are either bulk racking systems or cantilevered racks. Each pallet rack type serves its purpose such as drive-in/drive-thru racks, selective pallet racks, pallet flow racks, pushback pallet racks and cantilevered pallet racking.
3. Fixed Shelving
These systems aren’t designed to handle pallets. Rather, fixed shelving is a warehouse solution better applied for lighter products and multi-SKU applications. Fixed shelving units are also racks made of upright frames, however, their shelves serve a dual purpose as horizontal structures. You have two options with fixed shelving storage systems. One is wide-span shelving, which allows plenty of shelf access for products stored in bins and boxes. The other option is called industrial shelving, which offers many levels of adjustable storage in a small footprint.
4. Pallet Flow
Also known as carton-flow in the warehouse industry, this is a product storage system with a specific intention. This is a conveyer or deep-storage method where boxed products are stored in a first-in/first-out (FIFO) method. They’re delivered as-needed and have a fast recovery time suitable for high-throughput warehouses. Pallet, or carton-flow, storage systems are by far the most expensive warehouse storage systems. As such, only specialty warehouses employ pallet flow operations.
Most warehouse facilities commonly integrate a combination of pallet racks and fixed shelving. Your facility is likely no exception. You’ll undoubtedly want to make more use of vertical space than bulk or floor storage offers. But, if you’re unlikely to need or want to invest in some form of pallet flow system, you’re left with some attractive and affordable options.
Racking System Options
Don’t be confused between the terms “bulk storage systems” and “bulk racking systems.” Bulk storage is the basic floor-only option. It’s a significant space waster, and you’re likely going to want a better option for maximizing your warehouse efficiency. Bulk racking systems are a different matter. They still store bulky items, but they do it with vertical applications with pallets stacked in special-designed holding racks.
Bulk racking systems are also excellent solutions for storing products that aren’t palletized. That could be building materials such as lumber, pipes or rolled goods like carpets. For those long and bulky items, you’re best to invest in a specialty bulk racking system called cantilever racks.
Cantilever racks have horizontal metal arms extending from vertical uprights. They allow forklifts access to place or pick long products without having to disturb other goods stacked above or below. Many warehouses find cantilever racks the ideal space-saving solution. Cantilever rack systems come with different components, including:
- Single-sided cantilever towers: These are the vertical uprights or supports. Cantilever towers are the system’s backbone and create the general structure. Single-sided cantilever towers work best against a wall where only one-sided forklift access is necessary.
- Double-sided cantilever towers: For center-aisle access where your forklift needs pick and placement from both sides, double-sided cantilever towers are the way to go. This space-saving option turns your aisles into dual-purpose rows serving both sides of one passageway.
- Cantilever arms: These components are your horizontal members extending out from single or double-sided cantilever towers. They serve as shelves but only support a small part of the stored products. Sizing cantilever arms depends on how heavy your expected loads will be, how much room you have and what materials you’re serving. Large arms will support up to 3,000 pounds and extend 48 inches.
Having the right pallet racks also has a marked impact on your warehouse storage efficiency. They allow pallets to be stacked or slotted in similar arms that are sized and spaced specifically to house loaded pallets. You might be familiar with top brand names like Bulldog Rack, Husky & Wire and Unarco Rack. These strong and effective storage systems also offer you options like:
- Teardrop racks: These are easy to assemble systems that streamline installation. They employ teardrop-like punched holes for arm adjustment.
- Keystone racks: Their name comes from the upright hole shapes. Keystone racks are highly useful, effective and strong.
- Structural racks: For overall strength and durability, you may consider investing in structural racks. Besides holding countless pallets with heavy weights, they withstand the inevitable forklift impacts.
- Double-slotted racks: These are highly versatile warehouse racks. Because of the double-slotted upright design, they’re adaptable to other racking systems, making them true team players.
View Our Pallet Rack Selection
Shelving Storage Options
Another true payer for your warehouse efficiency team is industrial shelving. You’ll use industrial shelving in places where cantilever and bulk racks are impractical or unnecessary. That could be anywhere in your warehouse, and it might be one of the best small warehouse layout ideas.
With industrial shelving, you can organize any imaginable combination of loose or packaged products in an orderly and efficient manner. These commercial shelving units are extremely adaptable. They’ll quickly maximize your floor-to-ceiling space by incorporating accessory options like:
- Bins, totes and baskets
- Closed and open clipper shelving
- Multi-tiered, open and closed lockers
- Double and single wire Rivetrite shelving
Floor Plan Designs for a Warehouse
Choosing a warehouse layout design that works for your business can drastically improve operations. Some of the top designs you can choose from include:
- U-shaped design: A U-shaped warehouse has a semicircular layout. This floor plan design is ideal for warehouses of all sizes, given its ease of replication. To streamline operations, you can place loading and unloading areas next to each other with the reception behind them. On the other end will be the shipping bay. The back-end area of the warehouse can be used for storage.
- I-shaped design: This warehouse design looks like an “I” shape. It has a shipping area on one end, with the picking area behind it, and a loading and unloading area on the other end, with a reception behind it. The center of the warehouse is the storage area, meaning that products move from loading to storage to shipping, traveling the full length of the warehouse. This layout is best for warehouses with high-volume orders.
- L-shaped design: The traffic flow in this floor plan follows an “L” shape, making it great for warehouses with lots of storage needs. One side of the building has a loading and unloading area with a reception directly beside it. The adjacent side has a shipping and picking area, and the rest of the space in the middle is the storage area.
Factors to Consider When Deciding on Your Warehouse Layout
In addition to knowing all your options for storage equipment to maximize your warehouse efficiency, there are other factors to consider when deciding your warehouse layout. If you’re starting with the design of a new building, you’re really in the driver’s seat. You have the luxury of working with a warehouse design service expert like T.P. Supply Company, Inc., an international storage products and material handling equipment supply company. T.P. Supply Company, Inc. works with you throughout the warehouse design process to guarantee you maximum efficiency for your time and capital investment.
However, you’re likely not relocating to another facility, nor are you inclined to reduce profitable inventory to solve space problems. That leaves you with the most likely solution, and that’s to improve your existing facility layout. Here are some factors to consider:
- Existing structural components: You’ll already have some fixed structural elements in place including the exterior walls, doors and non-obstructing openings. You’ll also have interior support columns, stairs and non-bearing partitions. Look at each component as a help, not a hindrance. Work with them, not against.
- Aisle widths: This is an area where plenty of warehouse space is lost or gained, depending on design efficiency. By using the right bulk and cantilevered racks as well as the proper industrial shelving, you can easily add extra usable square footage at minimal cost.
- Vertical cubes: You’ll hear vertical cube as an industry standard when discussing warehouse organization and layout. This refers to maximizing your space in cubic volume from the floor up to the ceiling. By selectively placing stock from low to high, you’ll easily pick up extra space that’s efficient as well as valuable.
- Dock door placement: Your dock doors are fixed commodities that are expensive to relocate. It’s much more effective, not to mention less expensive, to design your aisles and storage systems around them. This is another area where a professional storage and material handling equipment company like T.P. Supply Company, Inc. can help you.
Tips for Maximizing Your Storage Space
Over the years, we’ve picked up a few storage space tips, and we’d like to pass these on to you:
- Place fast-moving products closest to your docks. This reduces travel time on workers and equipment.
- Store high-volume items at low levels and low-volume products high. This also reduces worker time as well as physical strain.
- Put bulk storage products against walls. This allows you to implement racks and shelves along aisles with dual-sided pick and place.
- Use your entire vertical cube effectively. It includes spaces above docks, offices, aisles and pick areas.
- Consider building mezzanines. These “second-floor” spaces are ideal for low-volume or out-of-season stock storage.
- Keep it simple. If you have a choice between a complex solution and a straight-forward one, keep it simple and maximize the most of what you’ve got. Remember that warehouse space accounts for 15 to 20 percent of your order costs.
Work With T.P. Supply Company, Inc. to Optimize Your Warehouse Space
T.P. Supply Company, Inc., has been in the warehouse supply business since 1979. Located in Mount Airy, N.C., we distribute storage solutions and material handling equipment throughout the United States, Canada and Mexico. We’d like to help you find storage solutions for all your warehouse space problems. You can call us at (877) 302-2337 or reach us anytime through our online contact form.